Sleipner launches two new simulators to improve occupational safety and reduce training costs by 66%
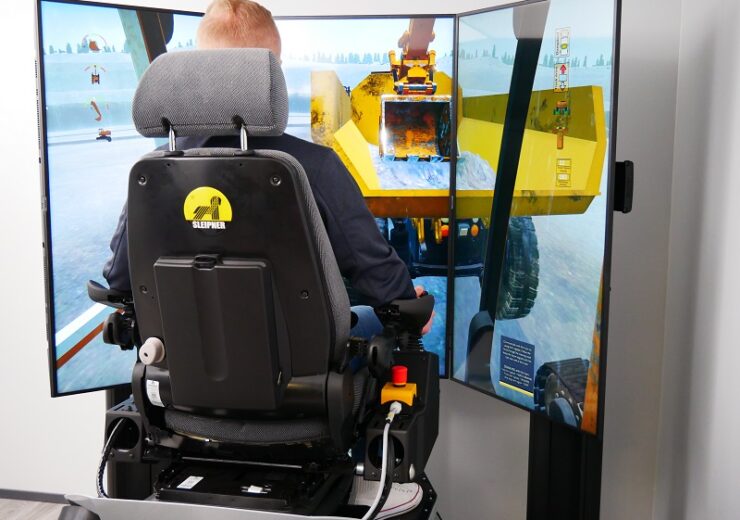
Sleipner simulator. (Credit: Sleipner Finland Oy)
Sleipner Finland Oy has taken the need for improving working safety and remote training to a new level with their E-series products. The company has launched both portable and static simulators to train excavator operators at mine and quarry sites.
The two new simulators have been created for different solutions. The portable simulator is light and movable, while the static simulator is a training station that is installed at the working site. With the simulators, operators can be trained on the new E-series products, or they can be retrained to maintain a certain quality level for operating the E-series. And since the world has changed more towards working remotely, the simulators create the possibility for completely remote training.
Sleipner has now completed testing at two mines in Finland with around 20 operators. The feedback from the operators was very good.
“For example, we trained excavator operators at the Boliden Kevitsa mine. Many of the attendees had variable working experience with excavators. The new simulator saved our customer almost two full days of valuable production time. Also, I noticed that both experienced older operators and younger “PlayStation generation” operators were able to learn on the simulator very quickly,” says Teijo Höylä, Product Manager at Sleipner.
Training with the simulator can reduce costs by 66% compared to traditional on-site training by saving fuel, maintenance and resources from productive work.
“The mine supervisors were happy that we were not taking machines out of production. Also, there was not a classroom of operators waiting for their turn on the simulator, so they could return to their work until their turn,” says Karl Marlow, Training Manager & Product Support at Sleipner.
“Normally we would do a classroom theory session with around 5 to 10 people pending on the mine production releasing operators. Then we could send some operators back to work and call them back for their turn on the simulator, as sometimes it can take up to an hour per operator,” Marlow describes.
Benefits from the simulator training can be sorted into four groups: work safety, increased training efficiency, increased productivity, and lower maintenance and training costs.
“The benefits to the customer include no losses in production from taking two machines out for training, no risk of accidents or incidents as the training takes place in a classroom instead of the mine area, and less lost time by not having operators just sitting around. Also, the level of operating skills required can be zero, meaning untrained operators spend more time on the simulator rather than posing a risk in the mine or pit. The one simulator can cover both small excavators and larger ones. Also, all the tasks we cover in theory and practice can be done on the simulator,” Marlow says.
If you have questions or are interested with the product, please do not hesitate to contact your local dealer or our sales department.
Boliden Kevitsa Mining Oy in Lapland, Finland, has already gained first-hand experience of training with the new Sleipner simulator. The practical training was arranged for operators of the Sleipner E190 excavator transport system, which Boliden acquired last autumn, while operators of the company’s mining trucks also participated in the theoretical part of the training. Boliden’s training supervisor Joni Ylinampa found the new simulator to be extremely useful, especially in terms of safety and cost.
“Sleipner was able to provide onsite training with its portable dual-screen simulator. It is always easier when the training comes to the customer instead of having to send our operators elsewhere. The first two five-person groups were trained on the simulator last autumn when there was already snow on the ground. Sleipner’s experienced trainer Karl Marlow was on hand throughout the training, and all the arrangements were very flexible. The service was really excellent in this respect,” Ylinampa says.
Advantage of simulators: safety issues can be practiced safely
Simulators provide operators with a risk-free experience of new equipment. In addition, good training significantly reduces the risk of accidents and damage to equipment.
“Accidents usually occur during initial training in real conditions, which naturally results in both production and financial losses – everything in this industry is big, including costs. If the vehicle’s brakes are used incorrectly and the machine breaks down as a result, it can cost tens of thousands of euros in an instant, as will a single tire. It is therefore essential to maximize the service life of our valuable machinery. Simulators also make it possible to practice for emergencies and other situations that can lead to a loss of control, so operators know how to respond in such events,” Ylinampa describes.
Driving feel is easy to find
Although it took a little time to get used to the simulator, and simulators never fully correspond to reality, Ylinampa reports that the operators found it easy to find an accurate driving feel.
“The Sleipner simulator is ideal for initial training, especially for operators who do not have previous experience with such excavator transport systems. Functionally, it demonstrates what modern technology can achieve. The simulator provides a really good driving feel, software and physics. The machines respond almost like in real life – it couldn’t be better. For example, the wheels of the transport system swing from the excavator bucket, just as they actually do. It is very realistic,” Ylinampa admits.
Improvement ideas from the participants included tweaking the software to allow them to continue the training programme from where they left off after fixing their mistakes instead of having to start all over from the beginning. Sleipner took note of this feedback immediately and has already made the necessary software updates.
“The last exercise in particular was quite challenging, as it is involved a twisty track. Participants had to really think and do all the right things. Impressively, everyone passed this test.”
Training has produced results
Since the training, operating the Sleipner E190 excavator transport system has gone well at Boliden, which uses the system to move a Komatsu PC2000 excavator.
“There have been no problems at any point. We were able to practice our basic skills with using the excavator transport system and to test the boundaries safely – keeping within these boundaries is essential for getting the job done. The simulator had different indicators to describe the angles of the machine, for example, so it showed clearly what would happen at too high a speed or if it was overturning,” says Ylinampa.
According to Ylinampa’s calculations, the simulator saved a lot of time. The training was faster as it allowed different operators to take the controls without any delay. Another advantage was that the training did not cause disruptions to operations at the mine due to traffic.
“Of course, training always takes time away from production, but with the simulator we needed a day or two less compared to training the old way. It also eliminated the need to prepare the work area for training by constructing tight curves, for example. The simulator gave our operators a strong basic understanding of the machine’s functions, so practicing in the field afterwards was much faster,” Ylinampa summarizes.
Source: Company Press Release