Around the world, mining operators are waking up to the potential value left in their waste products. The process of bioleaching, where microbes are used to extract valuable leftover metals from mine tailings, is a far more environmentally friendly process than the acids that have typically been used in the past. Nicholas Kenny speaks with Ross Orr, president and CEO of BacTech, and Radhakrishnan Mahadevan, professor at the Department of Chemical Engineering and Applied Chemistry, University of Toronto, to learn more about the benefits of this process can offer the mining industry.
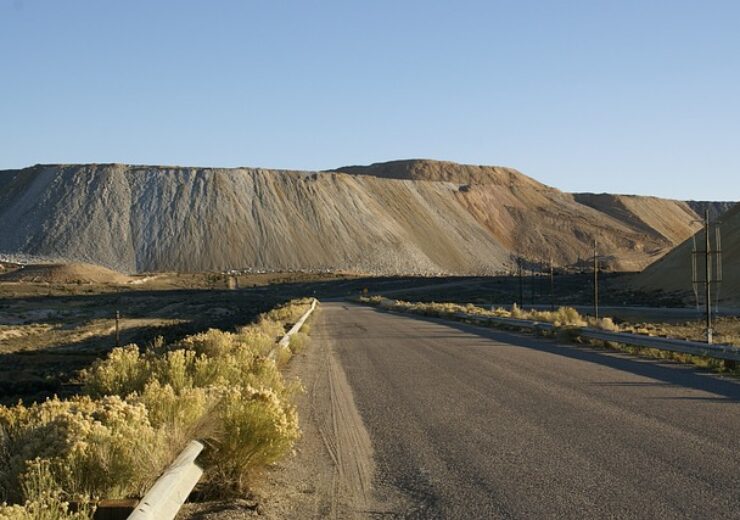
The process of bioleaching involves using microbes to extract valuable leftover metals from mine tailings. (Credit: WikimediaImages from Pixabay)
A by-product of the mining process, tailings present a significant challenge for the industry – both financially and in terms of sustainability and environmental impact. Usually taking the form of a liquid slurry made of water and fine metal or mineral particles, tailings can also be converted into dry-stack tailings, where the leftover material is compacted into a mound that is then able to be reclaimed by nature.
Typically, however, tailings have been stored in anoxic conditions underwater, as exposure to oxygen can result in chemical reactions that generate acid, capable of poisoning the surrounding environment. Even so, over time these pools will become highly acidic, often ranging from 1–3pH. These tailings pools or ponds are based within structures specifically designed to prevent the metals from leaching out into the surrounding environment – referred to as ‘tailings dams’. Tailings dams are one of the greatest risk factors in mining – essentially, they’re large bodies of contaminated water held back by concrete and metal, and any potential breach can cause massive damage.
Historically, some of the worst modern mining disasters have been due to tailings dam failures, most notably in Brumadinho, Brazil, in January 2019, which resulted in the deaths of 270 people and led Vale, the mining operator responsible, to agree to pay out over $7bn in compensation to those affected. Recently, there have been attempts to reduce reliance on water-based tailings storage, as elements of the industry turn to dry-stacking, which can reduce a mine’s water consumption and remove any chance of a catastrophic flood or other long-term storage issues. Yet, up until recently, this method wasn’t seen as cost-effective at scale, as the act of removing water from tailings for storage could be quite expensive.
Even if the industry stops requiring new water-based tailings storage facilities, the legacy tailings already in existence would continue to pose a problem. However, advances in bioleaching technology – where valuable metals are extracted from low-grade ore through the use of microorganisms – offer new ways to treat and remove the harmful material in fresh and legacy tailings, and to aid the reclamation of leftover metals from a mine’s waste products, boosting profitability and efficiency.
Speeding up natural processes
On the ground floor of this burgeoning space in mining is BacTech, an environmental technology company that specialises in bioleaching and remediation solutions. Its focus is on the processing and recovery of valuable metals like gold, silver, cobalt and copper, while transforming harmful contaminants like arsenic into benign products that can then be safely disposed of.
BacTech makes use of naturally occurring bacteria that is harmless to both humans and the environment to neutralise resource-rich mining sites – boosting both the environmental and economic situation through comprehensive metal recovery. These bacteria are typically microbes that are found to thrive naturally in tailings ponds – the resource-rich sites in question – capable of surviving in those hostile environments.
“Our tagline for the company is ‘Our bugs eat rocks’ because that was the easiest way to explain it to people,” notes Ross Orr, president and CEO of BacTech, with a laugh. “At the conferences we go to, that’s all we have on our booth – and sure enough, it does attract people.” To help explain how BacTech’s solutions function, Orr compares the process to a brick wall, where the bacteria target the mortar and separate metals and minerals into their core components.
In the company’s bioleaching process, ore concentrates are continually fed into the process, and, over a period of six days, the concentrate moves through a series of tanks, agitation and fertilisers to ensure that the bacteria function at a very high level. The concentrate is then broken down from what is referred to as an ‘arsenopyrite mineral’, with the iron and arsenic dissolving in the solution while the gold and silver remain as a solid, though are not yet amenable to conventional gold recovery.
“The sulphur would be the mortar I was talking about,” Orr explains, hearkening back to his brick wall comparison. “The acidic environment in the tanks is between 1.5–1.7pH, which ensure that any base metals or other metals that dissolve in acid, like arsenic, do so, and anything that doesn’t, like gold and silver, go in a separate direction at the end of the process.”
The next step is a solid/liquid separation where the gold and silver that have been liberated, go for conventional recovery to create a gold or silver doré bar for sale. The liquid now contains diluted base metals and other elements such as arsenic and iron, and is treated with limestone to raise the pH level. As the pH rises, ferric arsenate is precipitated from the liquid as gypsum – a benign form of arsenic that is dewatered and dry-stacked. “I like to say we’re the only nuts that go looking for arsenic, but it’s a big market,” adds Orr.
In Sudbury, BacTech is involved with a consortium to investigate the reprocessing of up to 100 million tonnes of pyrrhotite tailings that have been deposited in lakes around the area. Pyrrhotite is a sulphide mineral that is made up of iron (60%), nickel, cobalt and elemental sulphur. BacTech aims to sell the elemental sulphur removed from the process to the sulphuric acid industry, just as the iron extracted is sold to the steel industry. Beyond simply reclaiming valuable metals from waste products, however, applying bioleaching processes to pyrrhotite minerals also has the added benefit of destroying harmful sulphides.
“You’re eliminating potential acid mine drainage issues or acid rock issues, because you’re oxidising all of the sulphides,” Orr explains. “That’s why tailings are of interest to us. Because the stuff that was missed in the first go-around, through flotation, is the stuff in tailings that’s causing all the problems – eventually oxidising on their own just through nature and producing acid water [that can then leak] into the rivers.”
While a number of large companies have invested in bioleaching, such as Goldfields and Glencore, Orr has found that the mining industry as a whole has been slow to embrace the technology. “I’m constantly asked, ‘Why isn’t everybody using bioleaching?’” he notes. There are a couple of factors for this, however – the first being that bioleaching is still in its nascency in some ways, and can offer a slightly less effective recovery rate when it comes to gold, say, than traditional methods in roasting and smelting. For operations that might process half a million or so ounces of gold a year, a few percentages less in your gold recovery rate could mean tens of millions of dollars in lost revenue.
“Miners, if nothing else, are very good engineers and very cost-effective,” says Orr. “So, they tend to sort of plug their nose and stick to the conventional.” The advantage of bioleaching compared to traditional methods of recovery, however, is that it has a much lower environmental impact, and as the world continues to drive the importance of environmental, social and corporate governance (ESG) forward, the industry is slowly waking up to the solution’s benefits.
That’s not to say that bioleaching is an entirely new process, of course – the first bioleaching plant was built in the mid-1980s. Today, there are over 20 such plants worldwide, three of which were developed by BacTech under licencing deals. Now, however, the company is making moves into owning and operating its own plants, currently in the process of developing a facility in Tenguel – Ponce Enriquez, Ecuador, which is focused on processing high-grade concentrates and eventually tailings. The plant will be small enough to start with – capable of handling 50t per day (tpd), compared with a 2,000tpd operation in Kazakhstan run by Goldfields. The BacTech site will later be expanded to 200tpd in a second phase.
“Ultimately, it’s very simple – we’re using nature’s ability to do what it would normally do, but sped up from around 20 years to six days,” says Orr. “You might have to sacrifice a little profitability to do it cleaner than what you’ve been doing in the past, but that’s the way it is.”
Maximising microbial efficiency
While BacTech’s bioleaching solution makes use of naturally occurring bacteria, other groups, particularly in academia, have begun looking at modifying microbes to improve their bioleaching capabilities. One such group is based out of the University of Toronto, which has been collaborating with a group of mining firms to bioleaching processes for use in recovering nickel. While their focus is on enhancing bacteria through adaption evolution, the team of researchers are also developing similar processes using genetically engineered bacteria.
Led by Radhakrishnan Mahadevan, a professor in the Department of Chemical Engineering and Applied Chemistry at the University of Toronto, this research partnership with the Faculty of Applied Science and Engineering includes leading mining companies like Vale, Glencore, Metso-Outotec, MIRARCO, Yakum Consulting and, of course, BacTech.
The research partnership’s work all began with an investigation by Mahadevan and Vladimiros Papangelakis, professor of hydrometallurgy at the University of Toronto, looking into how biology could be applied to the mining industry – with particular focus on retrieving nickel from pyrrhotite tailings, an iron sulphide mineral. Attempting to characterise the microbial population found in pyrrhotite tailings, they went out to a tailings pond and retrieved the bacteria directly. From there, they began to enhance the microbes through adaptive evolution, gradually increasing the percentage of tailings solids present in the environments of samples that continued to grow well. Over time, this created new strains of microbes that were more effective at carrying out key chemical reactions.
“Once we were reasonably happy with the extent of growth, we looked at the microbes that were there present,” Mahadevan notes. “And to our surprise, [while] we were expecting many different kinds of microbes, it turned out that there was one kind of dominant microbe – over 90% of this culture was dominated by that one type of microbe.”
At that point, Mahadevan and his team carried out genome sequencing on that dominant microbe, attempting to identify the key genes at play. They were able to identify a new strain of a microbe known as Acidithiobacillus ferridurans, which they titled Acidithiobacillus ferridurans JAGS upon their publication of its full genome in 2020.
The team also started to look into ways to control the bioleaching process, engineering microbes not only to oxidise ferrous iron to ferric iron, but also to see if they could oxidise sulphides just to the point that elemental sulphur is left over as a by-product – rather than oxidising all the way to produce sulphates. This would help limit the amount of lime – calcium carbonate – required for neutralisation.
“In our initial techno-economic analysis is that with the nickel prices we were having, maybe a year and a half ago, the cost of [the bioleaching] process becomes viable only if you’re minimising the amount of neutralising agents that’s required,” says Mahadevan. “We just wanted to prevent the oxidation of sulphur to sulphate – that way you can control the process, get a valuable by-product, as well as try to see if we can leach the pyrrhotite tailings and then get nickel out.”
As with BacTech, the reasons for doing so are clear. There remains a significant amount of nickel in many tailings sites around the world, so being able to recover these extracts in a cost-effective manner has a clear economic benefit. Likewise, on the environmental side, legacy tailings present potential ramifications should the storage measures in place fail, and freshly generated tailings are still being created and placed in tailings ponds. Mahadevan’s team’s initial goal was to run these fresh tailings, rather than legacy tailings, through bioleaching processes with its microbes to demonstrate that they could isolate the valuable nickel and create an inert stream that doesn’t need to be stored in a tailings pond. As new tailings typically possess less nickel than their older counterparts – about 0.5% compared with approximately 1%, respectively, this was a considerable challenge.
“These inert tailings would be more environmentally friendly,” Mahadevan notes. “If you’re able to prove the concept on freshly generated tailings, then you can go back to these legacy tailings and then, hopefully, have an aspect of environmental clean-up.”
Eventually, if the bioleaching process can be optimised both in terms of cost-effectiveness and sustainability, he adds, not only would it be more appealing in the eyes of the mining industry, but some parts of the sector might start considering whether there are other high-energy consuming processes that could theoretically be replaced with biology.
“At this point, the mining industry hasn’t traditionally used biology in a big way, so maybe this is just the first opportunity,” says Mahadevan. “Eventually, there could be many other avenues where biology will be helpful.” For example, he notes that the current microbes his term are working with also have some potential to capture and store carbon, while improved methods of cleaning up legacy tailings and remediating tailings ponds could offer benefits from a sustainable water angle.
Delve into the DNA
Beyond their work evolving microbes through adaptation, Mahadevan and his team are also pursuing a genetic engineering approach by using the emerging gene editing technique known as CRISPR – an acronym for ‘clustered regularly interspaced short palindromic repeats’.
“These CRISPR-based tools can actually go in and specifically modify certain sections of the microbe’s DNA,” explains Mahadevan. “In a way, it’s basically accelerating the natural evolution.”
With his team’s work on adaptive evolution, they started with solutions containing 1% pyrrhotite solids, which the microbes from the tailings ponds could grow in. If they had been put immediately into a 20% solids solution, they would not survive. Slowly adapting the bacteria to a 5% solution over a six-to-eight-month period, however, was much more achievable, and over this time through evolution the bacteria accrued some sets of genes in larger numbers – the genes that helped them survive in more hostile environments, essentially.
“The question becomes, then, can we accelerate that process by which these things are naturally occurring by spurring them on in a more directed way?” Mahadevan asks. Using CRISPR, the research team intends to see if they can manipulate these genes to increase the ability of these microbes to be more resistant to environments with high percentages of tailings solids or boost their pH tolerance. At the same time, Mahadevan also highlights the potential for targeted modifications on the genes responsible for the oxidation of sulphur to sulphate.
While only having just started that process, the researchers have already released a publication demonstrating that, through modifying certain genes, they’ve been able to decrease the amount of sulphate produced through their bioleaching processes and instead form elemental sulphur.
“It’s not just about CRISPR,” he’s quick to note. “We’re still using the older methods that we’ve done before in the past. We want to do both. And we’ll see which ones lead to more interesting microbes, [which] we might potentially use in the future.”
Regardless of where the bacteria come from or how these microbes are created, they offer a truly fascinating potential to clean up some of the worst after-effects of the mining industry, removing harmful and difficult-to-store waste products and or to boost their safety and sustainability in areas surrounding a mine site. The mining sector might be a conservative one when it comes to embracing new developments, but if bioleaching solutions can boost their cost effectiveness and their efficiency when it comes to reclaiming metals and minerals, then they might well play a crucial role in reducing the industry’s environmental impact in the years ahead.
This article first appeared in World Mining Frontiers magazine.